
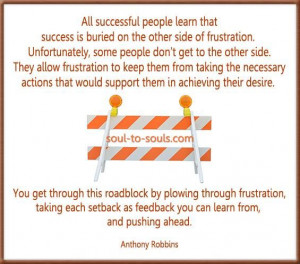
#Roadblock synonym full
The Production Manager in this example represents a personality that is sometimes encountered on project teams – someone who requires a level of control, involvement and acknowledgment in order to provide their full support. Although there was commitment to the project on the surface, the Production Manager’s approach was a roadblock for “true” implementation.
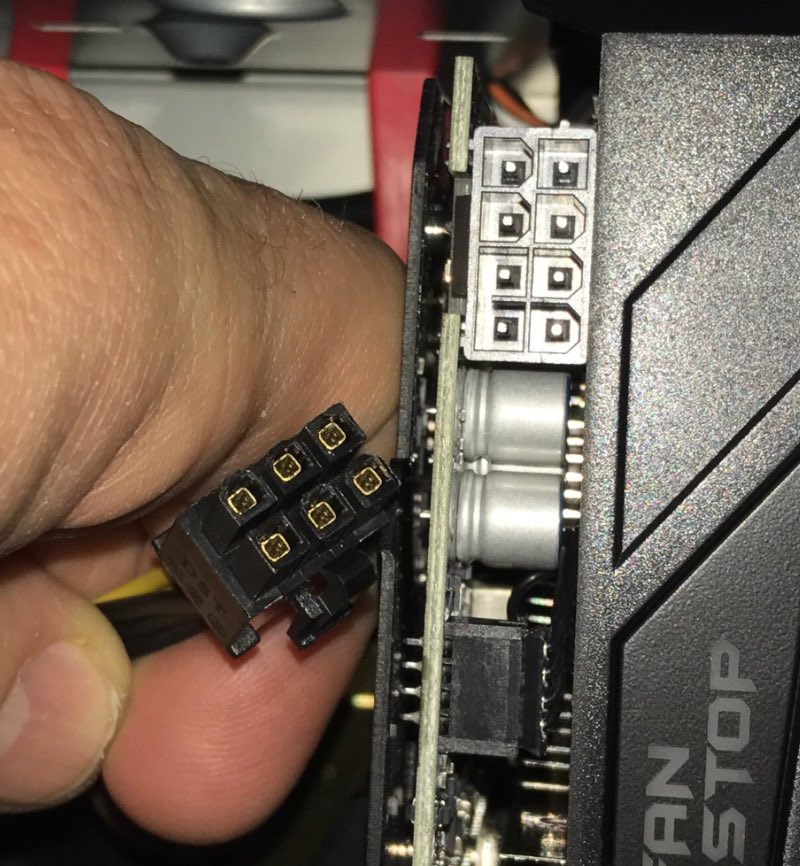
The project team members realized that in order for this project to progress, we needed to yield to the Production Manager’s plan. It was clear that if the team attempted to bring the operators in, the Production Manager would follow his original plan. He assumed that bringing the operators into the process would complicate matters by creating confusion with the added opinions and preferences. The rest of the project team believed that engaging the operators, understanding their needs, extracting their ideas and facilitating the approach to consistency were the way to gain the support of the users – key stakeholders in the process. The Production Manager instead believed that the users would adopt the new SW approach through deployment and training. Excluding Key StakeholdersĪlthough the Production Manager was on board with the project, he was adamantly opposed to including the operators on the team. His proposed approach was to take care of establishing the SW procedure himself and then roll out the document to the operators.

The users (operators) also were selected to participate on the team. As taught in project management and implementation best practices: “If you don’t have the Process Owner on board, you don’t have anything.” After getting buy-in from the Production Manager, the remainder of the project team was assembled from key representatives from aligned departments. When the project team was assembled, the Production Manager was an easy choice to be the Process Owner. All scheduling and updates were coordinated and approved by the Manager, making him a true Process Owner from a project definition perspective. Now let us fast forward 11 months, where the SW for the process finally gets implemented (correctly)! The details that follow are from the project team’s debriefing sessions, as we determined the causes for the extreme delay. I find the documenting of our findings to be therapeutic. It occurred to me that others must have experienced similar issues and that perhaps the reading of this piece will serve as the basis for some group therapy! The Project BeginsĪt the time of the project launch, the Production Manager was the most knowledgeable team member about the process under question, from historical and technical perspectives. He also had a good understanding of the capabilities of his department staff – a dozen operators on four separate teams who worked on alternating shifts. The value of trust was perfectly demonstrated in a Lean deployment project to rollout Standard Work (SW) for a key manufacturing process. The intent was to replace our existing standard operating procedure with a SW document to reduce variability, eliminate waste and provide a foundation for further improvement. The proposal sounded good to everyone on the management team and it was agreed that a SW document would be rolled out for the key manufacturing process within 30 days. One of those hard lessons was experienced by our company: learning how important trust is to establishing culture, changing mindsets and achieving true implementation – from picking the team members to beyond. As much as we try to avoid these pitfalls by following established methodologies or hiring experienced project management personnel, it remains clear that some of the best lessons are the ones we have to learn the hard way. There are many reasons for detours during your project journey unfortunately, many of these are unpredictable. Every Six Sigma project and Lean event goes exactly as planned right?
